For more than 25 years, we have been making FRP components for customers around the world.
When using FRP components you need to be sure that they will be of the highest quality. Technology developed over the span of more than 25 years and 2,000+ completed projects gives such assurance.
25+
Years on market
We have specialised in FRP fabrication for more than 2 decades.
2000+
Completed projects
In our industry, quality is experience. We have successfully executed over 2,000 various projects.
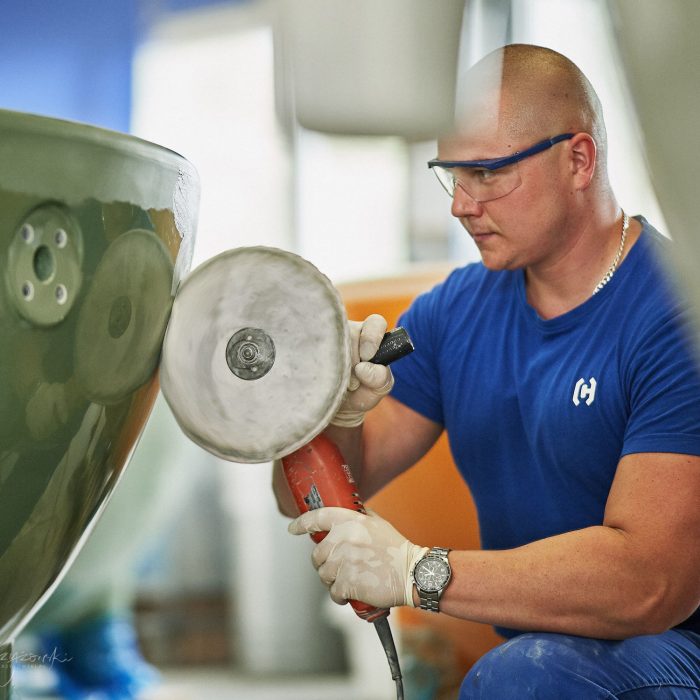