As mentioned in the previous post on lamination methods, at first you have to make a mold on which you will laminate your products. We will describe the molding process itself in details in one of the further posts.
The first step before manual lamination requires application of a mold release paste on the mold. This is a special paste that must be rubbed into the mold in order to facilitate molding of the product after the end of lamination and after obtaining the required hardness of the laminate.
Such a mold is then transferred for gel-coat painting purposes. The gel coat is an outer layer of our product. The modern technology allows using the gel coat in any RAL color. Before application, the gel coat must be mixed with a suitable amount of a hardener. The gel coat can be applied on the mold with the use of a brush or through spraying (with a special machine). The gel coat of a suitable thickness must be applied on the mold. The tickness of the gel coat is monitored while painting with a special measure, commonly referred to as “comb”.
When applied on the mold, the gel coat must be hard enough before you move to next stage, that is lamination. Too early initiated lamination leads to dissolution of the gel coat with a resin, which results in emergence of defects, e.g. “crocodiles”, discoloring, etc. on the surface of the product. When the gel coat is hard enough, you can start laminating.
Before application, the resin must be mixed with a suitable amount of the hardener. The amount of the hardener is very important and dependent upon numerous factors, such as temperature and humidity of the room in which you laminate. Too little hardener would cause too slow binding. Too much hardener would accelerate binding, which may hinder lamination, as well as cause bigger shrinkage, and consequently deviation of ready-made product dimensions from assumed standards. Adding the hardener to the resin causes the chemical reaction. The more hardener, the faster the reaction, and in effect higher the temperature. While dosing the hardener, you have to pay special attention to its quantity because excessive amounts may cause the resin and laminate to self-ignite.
After you have applied the gel coat, its surface must be greased with a resin on which you put a glass mat. Such a mat must be manually pressed with the use of a brush or roller until you fully soak the mat with resin. The order of applying resin and mat is crucial because it allows easier removal of air bubbles from the laminate. For this reason soaking the mat with resin is very important while producing laminates. Air bubbles that remain in the laminate weaken the laminate. They can also break and therefore cause damage to the outer layer of your ready -made product. In further steps you repeat the procedure by applying subsequent layers of the resin, mat and glass fabric. You can apply resin manually with the use of the brush or with the use of the spraying machine. After you have applied the required number of layers, you can finish lamination.
If you wish to ensure higher resistance to water, the raw part of the laminate can be covered in topcoat. Similar to get coat, you can apply this material manually with a brush. With regard to the top coat, identical to gel coat or resin, before you apply it, you need to add a suitable amount of the hardener. If you intend to make sure your product’s both sides are smooth and of high quality, you have to make two molds reflecting both sides of the product. This being the case, the aforementioned lamination is identical and simultaneous for both halves of the mold.
When dry, both halves of the mold are connected with the use of a special resin-based adhesive. Some products of this sort are filled with a special foam for stiffening purposes. Once the product has gone dry, it is removed from the mold and subject to further processing (grinding and finishing). The laminate becomes fully capable after the so-called tempering. Depending on the system (resin + hardener), the product is tempered for a specific period of time and at a specific temperature. Both these factors are interdependent, which means that the higher the tempering temperature, the shorter the period of time.
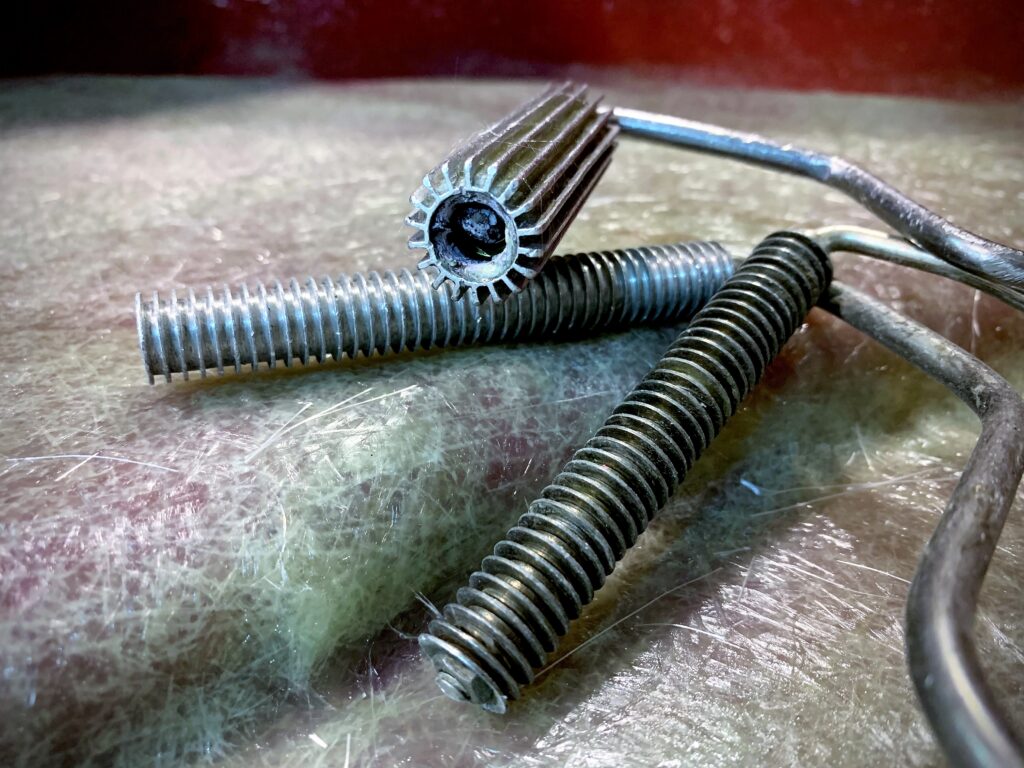
Photo 1 Rollers for manual production
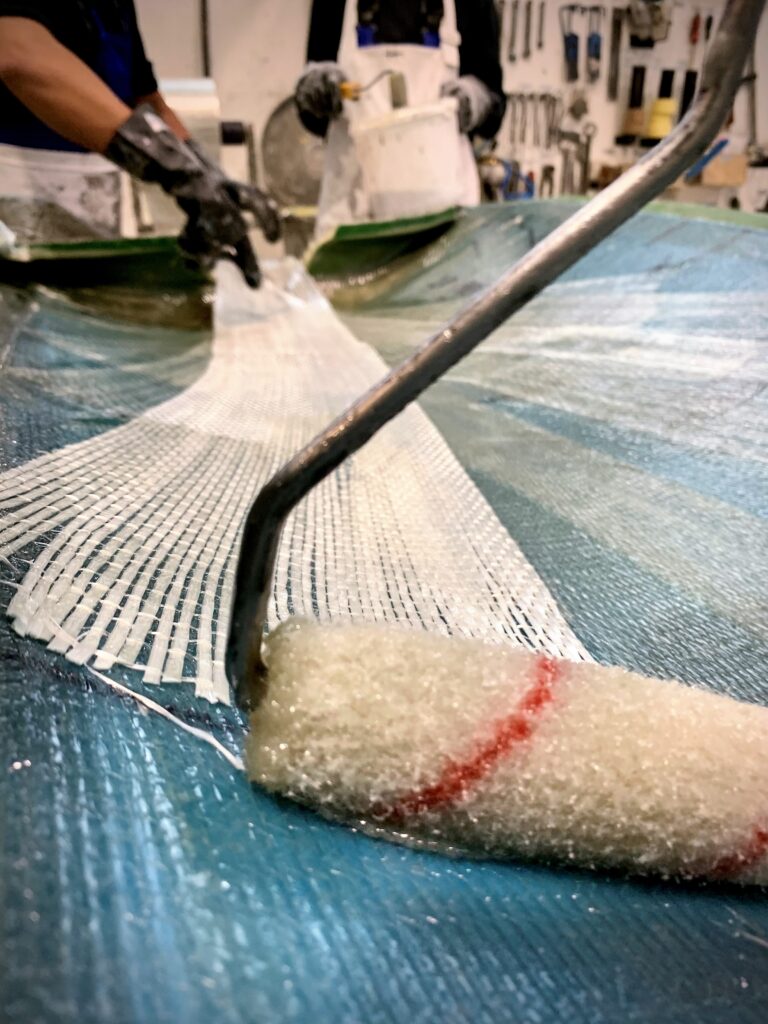
Photo 2 Roller during manual production

Photo 3 Roller with Chopped strand mat